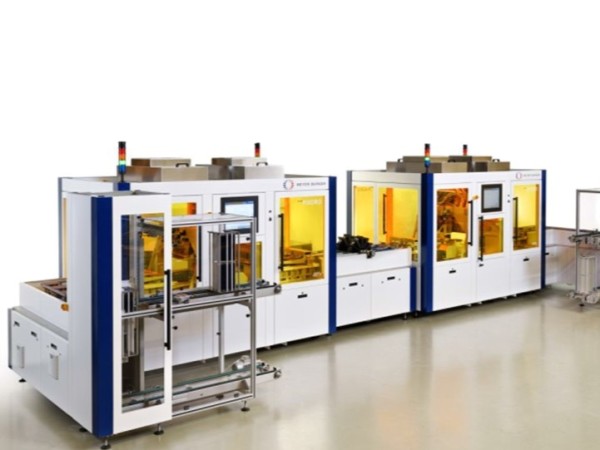
MEYER BURGER Phase-3 JETx-P Inkjet Printer System for 1200Wph, YoM2020
₹100,000.00
Meyer Burger Phase-3 JETx-P
Article number:
DV10089
Manufacturer:
Meyer Burger
Manufacturer number:
Phase-3 JETx-P
YoM:
2020
Condition:
New
Location

Deutschland
Availability:
ab sofort
Choose Quantity
Product Details
Meyer Burger (Netherlands) B.V. / Süss Phase-3 JETx-P Inkjet Printer Systems for 1200Wph
System description:
The PiXDROTM JETx-P inkjet printer is a mass production system specifically designed for photovoltaic applications. The JETx is a modular system that provides cost-effective, customized solutions for substrate handling, substrate handling, pre- and post-processing options, various throughput configurations and a range of control options.
Scope:
Automatically loaded wafer handler
- Compatible with Jonas & Redmann cassettes
- RFID cassette recognition
- In-line wafer thickness measurement module
- In-line module for measuring wafer size and wafer breakage
Inkjet printing station
- 2 wafer tracks, 2 chucks per track
- Software for individual wafer scaling and resolution correction
- 2 wafer preheating modules (one above each track)
- 4 heated wafer chucks with vacuum clamping
- Wafer edge alignment vision system
- Printhead unit with six KM1024i printheads (2 rows of 3 printheads each)
- 2 wafer drying modules after printing (one above each track)
- Automated ink supply with buffer tank and barcode identification
- Printhead maintenance module (rinse, wipe, spit and replace)
- Downward HEPA filtration for a clean processing environment
Automated optical inspection module:
- Customized image processing system for pattern recognition
- 2 line scan cameras with illumination modules (100% wafer inspection)
- Wafer handler
Miscellaneous:
- MES integration and license (see document "MES - Machine Interface, Version 3.0.22.1.0")
- Software interface to the Jonas & Redmann wafer handling module
- Installation and commissioning on site
- Operating and maintenance training (max. 1 week)
- User documentation for operation and basic maintenance (in English and German)
Notes:
Drying after printing:
The concept provides for heating the wafers after printing and includes an IR source and a dry air stream for solvent evaporation.
solvent evaporation. It assumes that the required drying time does not limit the overall throughput.
Coating thickness measurement:
The inline coating thickness measurement module offered is a spectral reflectrometer, type Sentech
FTPadv Inline. This device has not yet been qualified for the intended purpose. The qualification takes place
during the design and development phase.
Wafer preheating:
The concept is to heat the wafers with an IR source prior to printing. It assumes that the required
preheating time does not restrict the overall throughput.
Detection of wafer size and wafer breakage:
An additional high-resolution camera module is installed in the wafer handler module to measure the size of each individual wafer and possible damage.
Note on condition:
The system is unused and professionally packed in transport packaging.
System description:
The PiXDROTM JETx-P inkjet printer is a mass production system specifically designed for photovoltaic applications. The JETx is a modular system that provides cost-effective, customized solutions for substrate handling, substrate handling, pre- and post-processing options, various throughput configurations and a range of control options.
Scope:
Automatically loaded wafer handler
- Compatible with Jonas & Redmann cassettes
- RFID cassette recognition
- In-line wafer thickness measurement module
- In-line module for measuring wafer size and wafer breakage
Inkjet printing station
- 2 wafer tracks, 2 chucks per track
- Software for individual wafer scaling and resolution correction
- 2 wafer preheating modules (one above each track)
- 4 heated wafer chucks with vacuum clamping
- Wafer edge alignment vision system
- Printhead unit with six KM1024i printheads (2 rows of 3 printheads each)
- 2 wafer drying modules after printing (one above each track)
- Automated ink supply with buffer tank and barcode identification
- Printhead maintenance module (rinse, wipe, spit and replace)
- Downward HEPA filtration for a clean processing environment
Automated optical inspection module:
- Customized image processing system for pattern recognition
- 2 line scan cameras with illumination modules (100% wafer inspection)
- Wafer handler
Miscellaneous:
- MES integration and license (see document "MES - Machine Interface, Version 3.0.22.1.0")
- Software interface to the Jonas & Redmann wafer handling module
- Installation and commissioning on site
- Operating and maintenance training (max. 1 week)
- User documentation for operation and basic maintenance (in English and German)
Notes:
Drying after printing:
The concept provides for heating the wafers after printing and includes an IR source and a dry air stream for solvent evaporation.
solvent evaporation. It assumes that the required drying time does not limit the overall throughput.
Coating thickness measurement:
The inline coating thickness measurement module offered is a spectral reflectrometer, type Sentech
FTPadv Inline. This device has not yet been qualified for the intended purpose. The qualification takes place
during the design and development phase.
Wafer preheating:
The concept is to heat the wafers with an IR source prior to printing. It assumes that the required
preheating time does not restrict the overall throughput.
Detection of wafer size and wafer breakage:
An additional high-resolution camera module is installed in the wafer handler module to measure the size of each individual wafer and possible damage.
Note on condition:
The system is unused and professionally packed in transport packaging.