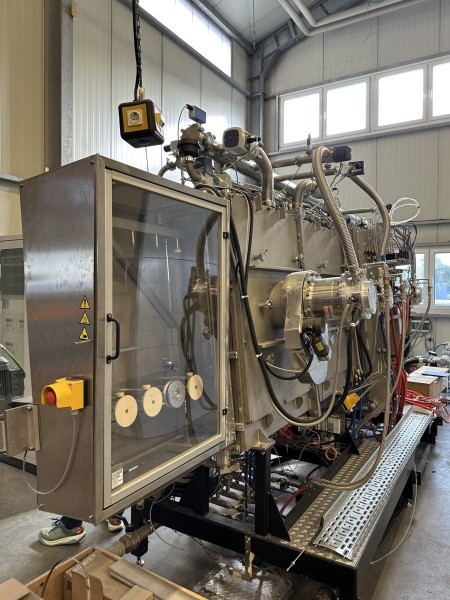
V 900, PVD system, vertical sputtering system, BJ2008
₹100,000.00
V 900
Article number:
DV10112
Manufacturer number:
V 900
Year of construction:
2008
Condition:
Used
Location:

Germany
Availability:
from now on
Choose Quantity
Product Details
Vertical sputtering system with magnetron sputtering for laboratory systems, V 900
Model: V900
Year of manufacture: 2008
General:
The LAB Tool V900 is a vertical sputtering system for laboratory applications.
The entire chamber is tilted. The carrier is driven by a bevel gear. The substrates can be transported with or without a carrier.
The carrier is guided on the top. In the case without a carrier, the glass rests on rollers. The lower edge of the glass remains at the same level with or without a carrier.
The changeover time for changing from one carrier to another should be less than 1 day, including readjustment and commissioning.
The temperature is up to 400°C.
In the LL, the glass is heated from the back and cooled from both sides. At PM1 and PM3, the glass is heated from both sides. At the PM2 (cathode), the glass is heated from the back.
At the PM, the entire glass moves from left to right and rotates back in front of the cathode during the coating process until the desired layer thickness is reached. The glass is heated during the process to keep the temperature uniform.
The glass bending is +/-3 mm maximum.
Basic features:
- Modular design based on 2 chamber types
Type A: load lock; load buffer
Type B: process and extension chamber with door for process equipment
- Chambers and carriers inclined by 6° (backwards)
- A substrate of up to 600 mm × 600 mm (HxL) can be placed on a carrier of 650 mm × 600 mm
- Loading/unloading of substrates from the front of the carrier
- The substrates are held by gravity (no fasteners)
- A spare magnetron position for later extensions
- PLC control. A PC is used for data recording
- System completely sealed with Viton rings (no rubber or silicone)
Module: LL
Application: Load lock
Turbopumps: Turbopump TMP-1503LM ISO 250 CE
2-point slide valve DN250: 1x pendulum valve type 16.2, DN 250
Backing pump: Dry vacuum backing pump SIHI GDV0400S**1K1
Module: PM
Application: Extension and process
Turbopumps: 2x Turbopump TMP-1503LM ISO 250 CE
Backing pump: Dry vacuum backing pump SIHI GDV0400S**1K1
Process gas: Ar, Ar/O2, adtl. Gas
MFC: 4
Power supply: SUMMIT 25/25 400/480 PFP YYLug 82A
Vacuum chambers:
Loading station LO
- Manual door
Loading lock module LL
Rectangular chamber made of stainless steel with water channels for cooling the chamber.
Internal dimensions: 850 mm × 1200 mm × 280 mm (L × H × D)
Chamber wall thickness: approx. 25 mm
Material: stainless steel DIN 1.4301 (standard hot rolled)
- 1 × service door on the front
- 1 × HV pump flange DN 250.
- 1 × forevacuum pump flange DN 63
- 3 × flanges for vacuum gauges and accessories.
- 1 × inspection window DN 63 on the top of the chamber.
- additional flanges for carrier drive, 2 spare flanges NW40, etc.
- 1 × pneumatically operated chamber door Dimensions: 80 × 1000 (W × H) Limit switch for the open/close position
Process module PM1 to PM3 (PM2 = sputtering)
Rectangular chamber made of stainless steel with water channels for chamber cooling.
Internal dimensions: 2450 mm × 1200 mm × 280 / 415 mm (L × H × T /D source)
Wall thickness of the chamber: approx. 25 mm
Material: stainless steel DIN 1.4301 (standard hot-rolled)
- 1 × process door for two magnetron cathodes (900 mm target length) Tilt drive with motor for cathode service.
- 2 × service door on the front
- 2 × HV pump flange DN 250
- 1 × forevacuum pump flange DN 63
- 5 × flanges with window for pyrometer (blind flange) per service door
- 4 × flanges for vacuum gauges and accessories.
- 3 × viewing opening DN 63 at the top of the chamber.
- additional flanges for vent valve, gas inlet, carrier drive, 3 spare flanges NW40, etc.
- 5 × set of chamber protection plates with 4 individual plates each
- 1 × pneumatically driven gate valve Dimensions: 80 × 1000 (W × H) Limit switch for open/closed position
Vacuum pumps and valves
- 1 × high vacuum gate valve DN250 ISO-K with pneumatic actuation
- 5 × pneumatically operated valve DN 40 (pre-vacuum turbo pump)
- 2 × pneumatically operated pre-vacuum valve DN 63
- 2 × electro-pneumatically operated valve DN 40 (vent valve)
- 1 × vent gas distribution in the chamber
Vacuum measuring devices
- 2 × Pirani transmitters, range: 10³ - 10-3 mbar
- 2 × Bayard-Alpert transducers, 10³ - 10-8 mbar
- 1 × with shut-off valve in PM
- 1 × Baratron transmitter, 0.1 mbar (1mbar mounted)
RGA
- RGA to be supplied by customer
- 1 × gate valve DN 40 CF (VAT) with extension piece
Carrier transport system (internal)
- 2 × ferrofluid sealed vacuum rotary unions, mounted electrically insulated
- 3 × servo motor drive
- 1 × light barriers to control the carrier position in LO (to be specified in detail)
- 6 × mechanical limit switches
Process equipment:
magnetrons
- 1 × tilting process door prepared for the installation of two magnetrons
- 2 × magnetron to be supplied by the customer
The dimensions of the flange are 1200 mm long and 600 mm wide with a pipe length of 900 mm. The pipe diameter is 133 mm. The door is closed with quick-release fasteners.
Process gas supply
- 4 × MFC (2×Ar, 2×O2, an additional gas to the central chamber inlet), with shut-off valve and filter for each MFC
Substrate heater:
substrate heating up to 400°C PM
- front and back (PM2 rear only) of the heating wall with inner and outer heating circuit, Inconel tubular heaters for heating substrates up to 300°C Radiation shielding on the back and front of the heating wall (uncooled), uniformity on the substrate ±10K
- 2 × IR pyrometer 0...400°C, for non-contact measurement of the substrate temperature, requires recalibration of the emissivity.
- Heating element shields in the process part
Substrate heating up to 200°C in LL
Front and rear heating wall with inner and outer heating circuit, Inconel tubular heaters for heating substrates up to 200°C
Radiation protection on the rear of the heating wall (uncooled)
Front and rear of the cooling plate
Cooling plates
* 2 × water-cooled cooling plates, installed in the LO
Media distributions
Cooling
water manifold Water distributor with separate water circuits:
1. Cathode 1
2. Cathode 2
3. Option
4. Sputter power supply(s) (multiple circuits)
5. Cooling plates
6. Vacuum chamber(s) (multiple circuits)
7. Turbo pumps
Circuit 1,2 with electrical flow indicator in the outlet, flow adjustment in each circuit.
Water blow-out device
For easy cathode changing, the cooling water can be blown out via manually operated valves.
Compressed air system
- Compressed air inlet unit with filter and pressure reducer
- PLC-controlled compressed air valve island for operating the valves
Cold water
- Inlet pressure: min. 5 bar, max. 7.0 bar (abs.)
- Outlet pressure: max. 1.5 bar (absolute)
Compressed air / gases
- Process gases at 2 ... 3 bar, max. 500 sccm
- dry compressed air at 5 bar
Electrical power
- 400 V ± 10 %
- 50 Hz ± 3 %
- 5-wire system (3 × phase, zero, protective earth)
- Nominal power approx. 120 kW
automatic residual current circuit breaker installed in the network
Model: V900
Year of manufacture: 2008
General:
The LAB Tool V900 is a vertical sputtering system for laboratory applications.
The entire chamber is tilted. The carrier is driven by a bevel gear. The substrates can be transported with or without a carrier.
The carrier is guided on the top. In the case without a carrier, the glass rests on rollers. The lower edge of the glass remains at the same level with or without a carrier.
The changeover time for changing from one carrier to another should be less than 1 day, including readjustment and commissioning.
The temperature is up to 400°C.
In the LL, the glass is heated from the back and cooled from both sides. At PM1 and PM3, the glass is heated from both sides. At the PM2 (cathode), the glass is heated from the back.
At the PM, the entire glass moves from left to right and rotates back in front of the cathode during the coating process until the desired layer thickness is reached. The glass is heated during the process to keep the temperature uniform.
The glass bending is +/-3 mm maximum.
Basic features:
- Modular design based on 2 chamber types
Type A: load lock; load buffer
Type B: process and extension chamber with door for process equipment
- Chambers and carriers inclined by 6° (backwards)
- A substrate of up to 600 mm × 600 mm (HxL) can be placed on a carrier of 650 mm × 600 mm
- Loading/unloading of substrates from the front of the carrier
- The substrates are held by gravity (no fasteners)
- A spare magnetron position for later extensions
- PLC control. A PC is used for data recording
- System completely sealed with Viton rings (no rubber or silicone)
Module: LL
Application: Load lock
Turbopumps: Turbopump TMP-1503LM ISO 250 CE
2-point slide valve DN250: 1x pendulum valve type 16.2, DN 250
Backing pump: Dry vacuum backing pump SIHI GDV0400S**1K1
Module: PM
Application: Extension and process
Turbopumps: 2x Turbopump TMP-1503LM ISO 250 CE
Backing pump: Dry vacuum backing pump SIHI GDV0400S**1K1
Process gas: Ar, Ar/O2, adtl. Gas
MFC: 4
Power supply: SUMMIT 25/25 400/480 PFP YYLug 82A
Vacuum chambers:
Loading station LO
- Manual door
Loading lock module LL
Rectangular chamber made of stainless steel with water channels for cooling the chamber.
Internal dimensions: 850 mm × 1200 mm × 280 mm (L × H × D)
Chamber wall thickness: approx. 25 mm
Material: stainless steel DIN 1.4301 (standard hot rolled)
- 1 × service door on the front
- 1 × HV pump flange DN 250.
- 1 × forevacuum pump flange DN 63
- 3 × flanges for vacuum gauges and accessories.
- 1 × inspection window DN 63 on the top of the chamber.
- additional flanges for carrier drive, 2 spare flanges NW40, etc.
- 1 × pneumatically operated chamber door Dimensions: 80 × 1000 (W × H) Limit switch for the open/close position
Process module PM1 to PM3 (PM2 = sputtering)
Rectangular chamber made of stainless steel with water channels for chamber cooling.
Internal dimensions: 2450 mm × 1200 mm × 280 / 415 mm (L × H × T /D source)
Wall thickness of the chamber: approx. 25 mm
Material: stainless steel DIN 1.4301 (standard hot-rolled)
- 1 × process door for two magnetron cathodes (900 mm target length) Tilt drive with motor for cathode service.
- 2 × service door on the front
- 2 × HV pump flange DN 250
- 1 × forevacuum pump flange DN 63
- 5 × flanges with window for pyrometer (blind flange) per service door
- 4 × flanges for vacuum gauges and accessories.
- 3 × viewing opening DN 63 at the top of the chamber.
- additional flanges for vent valve, gas inlet, carrier drive, 3 spare flanges NW40, etc.
- 5 × set of chamber protection plates with 4 individual plates each
- 1 × pneumatically driven gate valve Dimensions: 80 × 1000 (W × H) Limit switch for open/closed position
Vacuum pumps and valves
- 1 × high vacuum gate valve DN250 ISO-K with pneumatic actuation
- 5 × pneumatically operated valve DN 40 (pre-vacuum turbo pump)
- 2 × pneumatically operated pre-vacuum valve DN 63
- 2 × electro-pneumatically operated valve DN 40 (vent valve)
- 1 × vent gas distribution in the chamber
Vacuum measuring devices
- 2 × Pirani transmitters, range: 10³ - 10-3 mbar
- 2 × Bayard-Alpert transducers, 10³ - 10-8 mbar
- 1 × with shut-off valve in PM
- 1 × Baratron transmitter, 0.1 mbar (1mbar mounted)
RGA
- RGA to be supplied by customer
- 1 × gate valve DN 40 CF (VAT) with extension piece
Carrier transport system (internal)
- 2 × ferrofluid sealed vacuum rotary unions, mounted electrically insulated
- 3 × servo motor drive
- 1 × light barriers to control the carrier position in LO (to be specified in detail)
- 6 × mechanical limit switches
Process equipment:
magnetrons
- 1 × tilting process door prepared for the installation of two magnetrons
- 2 × magnetron to be supplied by the customer
The dimensions of the flange are 1200 mm long and 600 mm wide with a pipe length of 900 mm. The pipe diameter is 133 mm. The door is closed with quick-release fasteners.
Process gas supply
- 4 × MFC (2×Ar, 2×O2, an additional gas to the central chamber inlet), with shut-off valve and filter for each MFC
Substrate heater:
substrate heating up to 400°C PM
- front and back (PM2 rear only) of the heating wall with inner and outer heating circuit, Inconel tubular heaters for heating substrates up to 300°C Radiation shielding on the back and front of the heating wall (uncooled), uniformity on the substrate ±10K
- 2 × IR pyrometer 0...400°C, for non-contact measurement of the substrate temperature, requires recalibration of the emissivity.
- Heating element shields in the process part
Substrate heating up to 200°C in LL
Front and rear heating wall with inner and outer heating circuit, Inconel tubular heaters for heating substrates up to 200°C
Radiation protection on the rear of the heating wall (uncooled)
Front and rear of the cooling plate
Cooling plates
* 2 × water-cooled cooling plates, installed in the LO
Media distributions
Cooling
water manifold Water distributor with separate water circuits:
1. Cathode 1
2. Cathode 2
3. Option
4. Sputter power supply(s) (multiple circuits)
5. Cooling plates
6. Vacuum chamber(s) (multiple circuits)
7. Turbo pumps
Circuit 1,2 with electrical flow indicator in the outlet, flow adjustment in each circuit.
Water blow-out device
For easy cathode changing, the cooling water can be blown out via manually operated valves.
Compressed air system
- Compressed air inlet unit with filter and pressure reducer
- PLC-controlled compressed air valve island for operating the valves
Cold water
- Inlet pressure: min. 5 bar, max. 7.0 bar (abs.)
- Outlet pressure: max. 1.5 bar (absolute)
Compressed air / gases
- Process gases at 2 ... 3 bar, max. 500 sccm
- dry compressed air at 5 bar
Electrical power
- 400 V ± 10 %
- 50 Hz ± 3 %
- 5-wire system (3 × phase, zero, protective earth)
- Nominal power approx. 120 kW
automatic residual current circuit breaker installed in the network